For data centers downtime is not an option. Yet many facilities still rely on a reactive approach to maintenance — responding to issues only after they arise. The break/fix model may seem cost-effective in the short term, but it exposes data center operators to unnecessary risk, inefficiencies, and unplanned costs.
The Impact on Data Center Operators
Data center executives are under constant pressure to balance uptime, operational costs, and long-term asset performance. However, when maintenance strategies are reactive, they become a liability. Teams overlook minor equipment degradation until it causes critical system failures. Emergency repairs pull staff away from other essential duties and often require rush shipments or costly vendor dispatches.
This approach not only increases direct maintenance costs but also creates a ripple effect:
- Higher risk of downtime and SLA breaches
- Unpredictable budgeting due to unplanned expenses
- Accelerated asset depreciation and reduced lifecycle value
- Reduced team productivity caused by constant firefighting
Reactive maintenance also complicates planning and erodes confidence across the organization. Financial leaders can’t forecast accurately. Operations leaders lack the data to make strategic upgrades. Executive stakeholders wonder whether their infrastructure is truly reliable.
Shifting Toward Predictive Maintenance
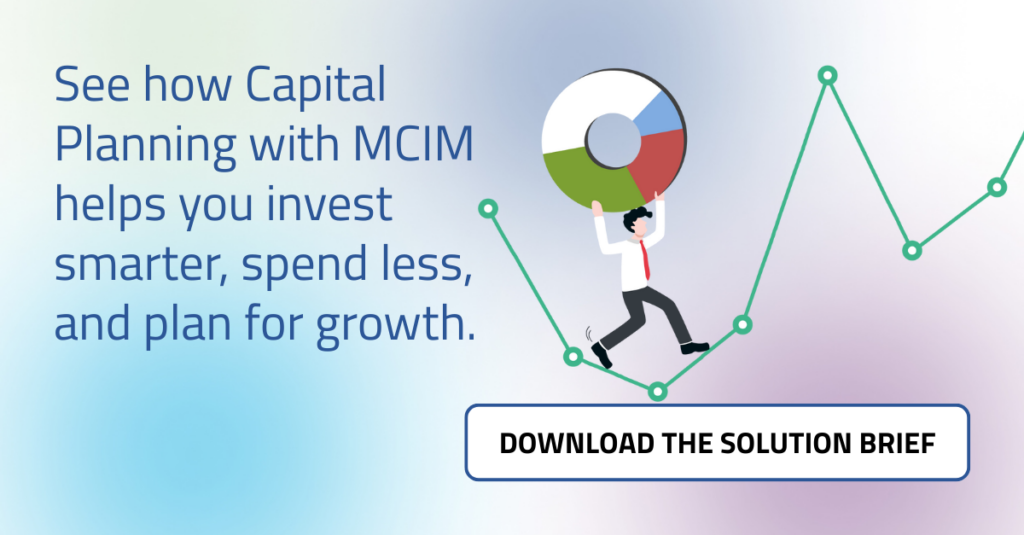
Modern data centers must evolve to stay ahead of risk. Predictive maintenance is the next step in this evolution. By using data to anticipate failures before they occur, operators can reduce unplanned downtime, optimize resource allocation, and extend the life of critical infrastructure.
How MCIM Helps
MCIM empowers data center teams to move beyond break/fix by enabling a proactive, data-informed maintenance strategy:
- Asset Management Module: Tracks asset age, condition, and service history, providing visibility into wear patterns and upcoming service needs. Executives gain portfolio-level insights into which systems are at greatest risk and which are performing above expectations.
- Monitoring Module: Integrates sensor and BMS data to surface performance anomalies, temperature deviations, or early-warning indicators, enabling teams to address issues before they escalate. This real-time feedback loop is essential for executives tasked with reducing risk.
- Incident Management Module: Aggregates and analyzes past incidents to identify recurring problems, correlate with asset types, and detect root causes. Executives benefit from better trend analysis and reduced incident frequency over time.
- Work Module: Supports the automation of scheduled preventative maintenance and escalates recurring issues for deeper review. As teams implement predictive processes, executives can shift maintenance budgets from reactive spend to strategic investments.
With MCIM, facilities teams move from a reactive firefighting posture to a forward-looking operational model. Predictive maintenance isn’t just a tool for technicians—it’s a strategic advantage that enables smarter capital planning, stronger uptime SLAs, and a culture of continuous improvement.
To schedule a demo or speak with a member of our team, please visit: https://www.mcim24x7.com