When uptime and reliability directly impacts revenue and productivity, maintaining continuity and resilience is fundamental. Traditional maintenance methods such as scheduled maintenance and run-to-fail are risky. These methods are not sufficient for maintaining the unseen critical assets that are essential for smooth operations. Advances in data collection and analysis have made predictive maintenance more popular, saving money on labor, spare parts, and equipment costs.
Unplanned vs. Preventive vs. Predictive Maintenance Defined
Unplanned maintenance is reactive break/fix work conducted when problems unexpectedly arise, often requiring emergency repairs during crucial operating hours. Also called run-to-failure or reactive maintenance, this is done to save on labor and spare part costs.
Depending on last-minute repairs to delay costs can lead to more problems in the long run. Critical equipment may break down more often, last for a shorter time, and require more expensive fixes when they do fail. Not to mention the potential impact a critical failure may have on your facility’s operations.
Preventive maintenance, also known as scheduled or planned maintenance, takes a structured, proactive approach to caring for assets. Regularly scheduled preventive maintenance at predefined intervals aims to identify potential problems early and address them preemptively. These schedules are usually based on manufacturer recommendations, industry best practices, or internal maintenance plans. Scheduled upkeep can minimize unplanned downtime, enhance equipment reliability, and increase asset lifespan as issues are addressed proactively.
However, planned maintenance doesn’t consider real-time conditions or early signs of equipment failure that predictive maintenance solutions can detect. Scheduled maintenance can also lead to unnecessary services that cost time and resources and introduce increased risk in asset reliability. With 70% of outages being caused by human error, the fewer chances someone has to make a mistake, the better.
Predictive maintenance is a proactive approach that utilizes data and technology to predict when equipment is likely to fail. This allows maintenance activities to be performed when needed but before it fails and impacts operations. This condition-based maintenance helps efficiently allocate maintenance resources, minimize downtime and service disruptions, and extend an asset’s lifespan by addressing issues before they can cause failure.
The Critical Benefits of Predictive Maintenance
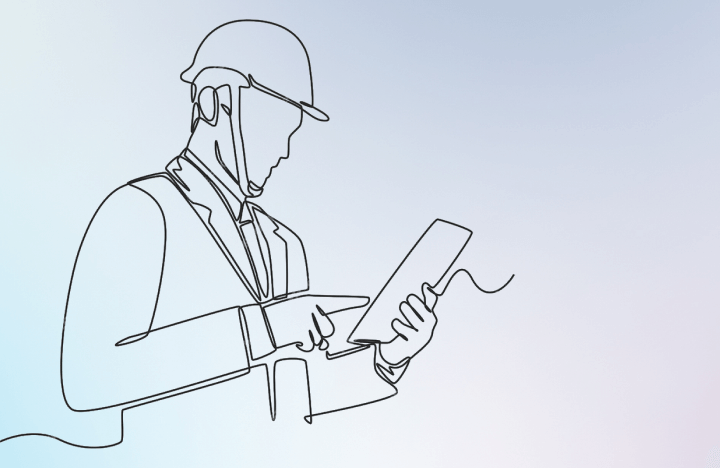
Facilities use predictive maintenance to balance reliability and cost-efficiency by harnessing real-time, clean, curated, and connected data to make maintenance decisions. The advantages include:
Increased Equipment Uptime: Using predictive maintenance, facilities can address problems proactively, significantly reducing downtime and maintaining high equipment availability, ensuring smooth and uninterrupted operations.
Cost Savings: Facilities can avoid unnecessary, scheduled maintenance and reduce the expenses associated with emergency repairs, spare parts, and overtime labor.
Extended Asset Lifespan: Proactively addressing issues and maintaining equipment in optimal condition can extend the lifespan of critical assets, resulting in a longer ROI and reduced capital expenditure on replacements.
Improved Safety: Facilities can address safety-related issues promptly and in advance, preventing accidents and injuries associated with equipment breakdowns.
Better Resource Allocation: By performing maintenance tasks when necessary, facilities can reduce idle time and maintenance costs associated with scheduled maintenance that may not be required.
Data-Driven Decision-Making: A data-driven approach provides valuable insights into the condition of assets, allowing facilities to make informed decisions about maintenance strategies, replacement timing, and operational improvements.
Customized Maintenance Schedules: Facilities can tailor maintenance schedules to the actual condition of each asset. Maintenance tasks can be performed when data indicates they are needed, rather than relying on fixed intervals, optimizing asset management and performance, and reducing operational disruptions.
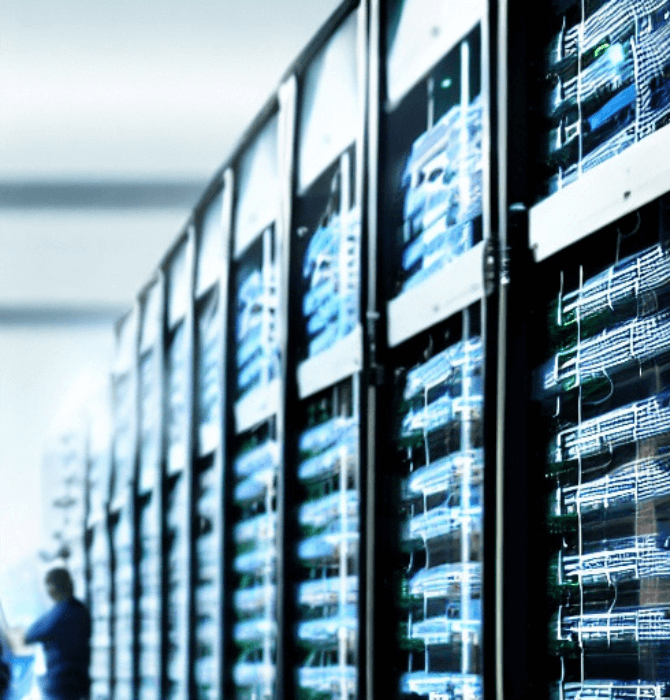
Predictive Risk Management:
Lowering Incidents 84% with MCIM
With MCIM, one top-tier data center was able to use predictive risk management to slash its critical incidents by 84% in just 18 months.
Creating an Effective Predictive Maintenance Strategy
Creating an effective predictive maintenance program involves several critical steps to ensure the successful implementation and operation of the program. Here are the key steps to follow:
- Focus on the Right Assets: Not all assets may require predictive maintenance work, so focus on those that significantly impact your operations and can benefit from predictive maintenance.
- Data Collection and Sensors: Install appropriate sensors and data collection systems and procedures on the selected assets. Ensure the data collected is accurate, reliable, and accessible in real time.
- Integrate Data and Analysis in a Central Platform: Integrating your operational data across your portfolio into a single system allows you to standardize your data and ensure it is clean, accurate, and available in real-time. This system should be able to analyze your data and metrics to detect patterns, anomalies, and early signs of equipment degradation or failure. Using a single system means that data is available through clear dashboards that can inform executives and operators on the status of their entire portfolio in real time.
- Use Asset Reliability Benchmarking to Establish Baselines: Cross-referencing your facility’s data with industry and global asset reliability benchmarking allows you to see how your assets perform against industry averages. With this information, you can create baseline performance profiles for each asset and make a reference point for deviations and issues.
- Condition Monitoring: Continuously monitor the condition of your assets in real time. Use alerts and notifications to trigger maintenance actions when anomalies are detected.
- Maintenance Planning: Use the insights from your predictive maintenance system to plan and schedule maintenance activities. Ensure that maintenance actions align with the asset’s actual condition and prioritize tasks based on criticality.
- Spare Parts and Resources: Being able to predict when and how an asset will fail empowers facilities to maintain an inventory of critical spare parts and ensure maintenance teams have the necessary resources and training to execute the required tasks efficiently.
- Documentation and Reporting: Thoroughly document maintenance activities, including work orders, task completion, and results. All this information should be stored directly in the asset’s records, making them available anytime from anywhere, even in the field via mobile devices.
Your Facility’s Predictive Maintenance Strategy
Mission-critical facility operations leave no room for disruptive unplanned downtime. Implementing a data-driven approach that harnesses real-time sensor data and advanced analytics allows facility operators to detect early signs of equipment degradation or impending failures. This proactive strategy allows for timely interventions, reducing the risk of unexpected downtime and costly disruptions to critical services.
Powerful platforms like MCIM help optimize maintenance planning, scheduling, and work order management, improving compliance while limiting human-error and keeping your data clean. Prioritizing Predictive Maintenance is must for any facility seeking to maintain high uptime, meet service level agreements, and stay ahead of potential issues that may impact the facility’s mission-critical operations.